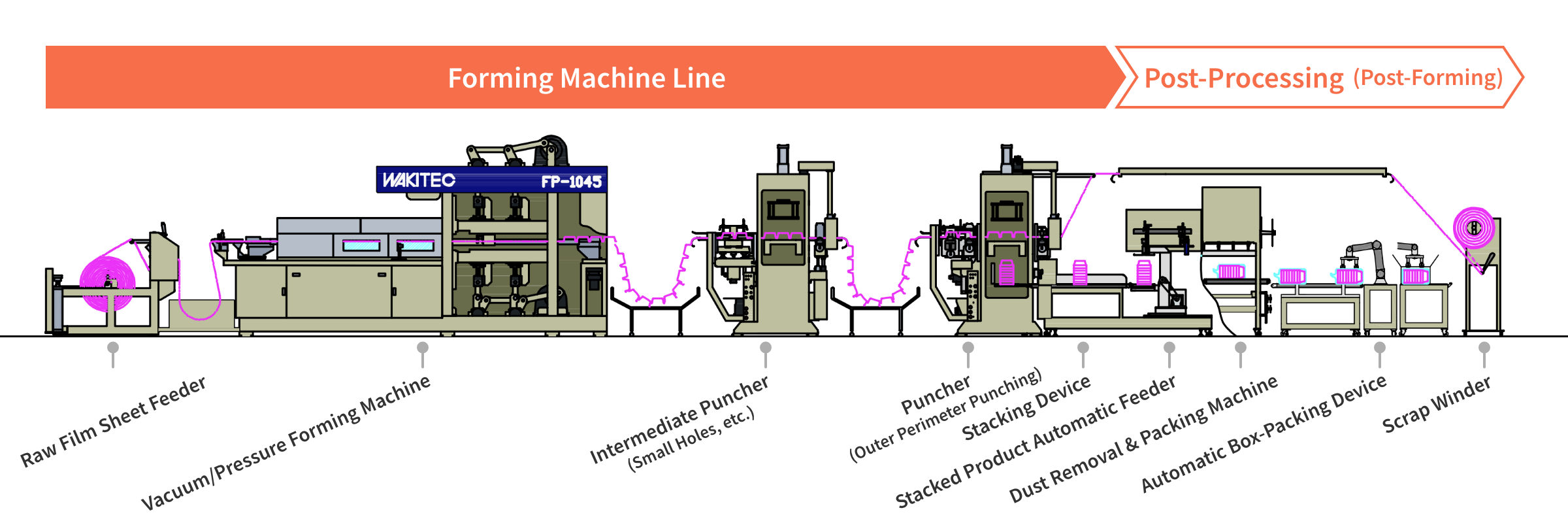
Discover how WAKITEC’s products, including our forming machines, punchers, dust-removal and packing machines, are used within the manufacturing line and other processes. Explore a simple visualization of the integrated process from supply of materials to completion of finished products, encompassing forming, trimming, stacking, and packing, and the supporting roles played by WAKITEC’s machines.
Forming Machine Line: Forming Process & Post-Processing
The forming machine line is an efficient manufacturing system that automates the integrated process from supply of materials to forming, trimming, and stacking of products. In addition, a rapidly growing area of recent demand is referred to as “post-processing”: dust removal, packing, box-packing, and other processes that are performed after products are manufactured. Particularly within Japan, where we face a declining population, the question of how to implement “labor-saving” and “automation” in post-processing, an area conventionally performed by human operators, is a major challenge.
Forming Process (Forming Machine Line) |
Post-Processing (Post-Forming) |
|||
---|---|---|---|---|
Forming |
Trimming |
Stacking |
Dust Removal Packing |
Box Packing, etc. |
Thermoplastic resin sheets are heated using a heater and formed into shape with a mold. Depending on the product shape, additional processes such as cooling may be performed to complete the final product. Vacuum forming is typically used for products with standard shapes. However, when more sharply defined shapes are required, vacuum pressure forming is used. In addition, different forming machine types are used for different sheet materials. In particular, OPS materials require the use of hot plate pressure forming machines. | Next, the products formed in the sheet are cut out from the sheet (trimming) using a puncher. However, since the main puncher performs outer perimeter punching, if small holes or perforations are required within the product, an intermediate puncher must be positioned before the main puncher to perform these operations. After trimming, the leftover sheet (skeleton) is wound by the scrap winder, facilitating the subsequent processing. | Each trimmed product is collected (stacked) in the operator’s desired quantities, and fed out from the machine. This process marks the product’s initial stage of completion. | Any dust, debris, hair, or other contaminants that become mixed into the completed products will cause significant inconvenience for the end user. Therefore, each individual product must undergo dust removal processing to ensure safe and reliable products. WAKITEC offers high-performance dust removal machines equipped with dedicated dust blowers combined with destaticizing devices, packing machines that automate the conventionally labor-intensive packing process, and dust removal & packing machines that combine the functions of both. Additionally, our stacked product automatic feeder, which automatically transfers products from the stacking device to the dust removal and packing machines, is recently receiving a large number of inquiries. | The final processing operation is box packing. WAKITEC offers an automatic box-packing device utilizing a collaborative robot, in addition to an automatic device that semi-automate the fabrication of cardboard boxes used in the packing process. Please feel free to inquire about these devices. |
Selecting a Machine
Forming Machine Line
Selecting a Forming Machine
The best way to select an optimal forming machine is to decide what shape and what size products you want to make, which materials you will use, what quantity you want, and how quickly. At WAKITEC, we begin by asking our customers these questions.
Even so, there are several standard patterns, a few of which we will introduce below. (Please note that many products do not follow these patterns; please feel free to discuss your needs with us.)
Food Containers
In general, when manufacturing food containers, the deciding factor is often “how quickly can we make a large quantity of products.” In such cases, a forming machine capable of large width and length (feed) and high speed conveyance is needed. Additionally, when using OPS materials, a hot plate forming machine is optimally suited.
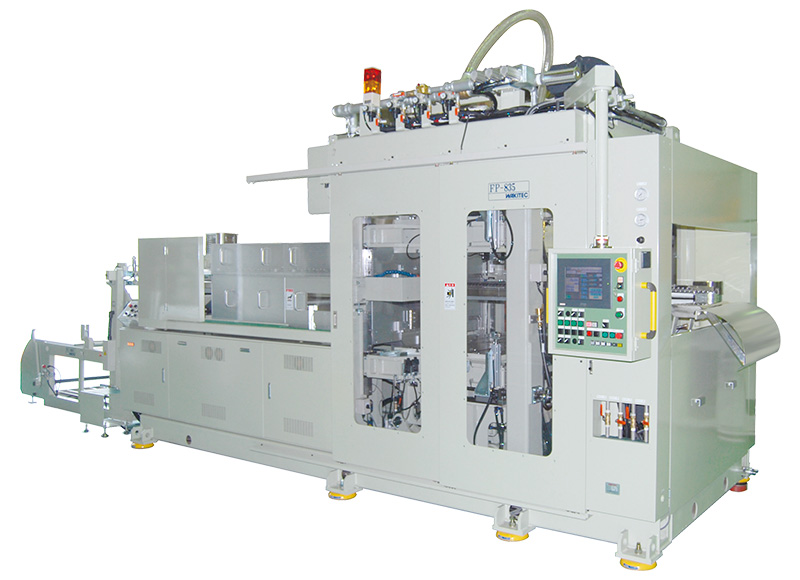
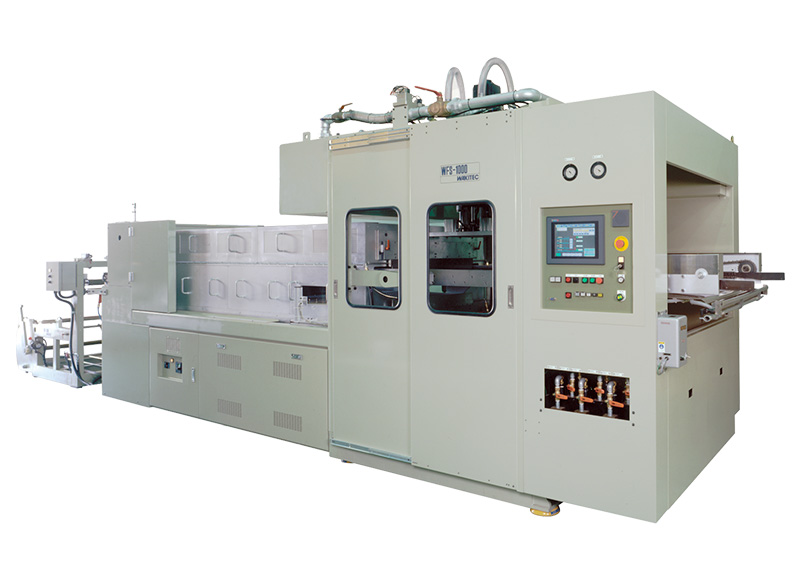
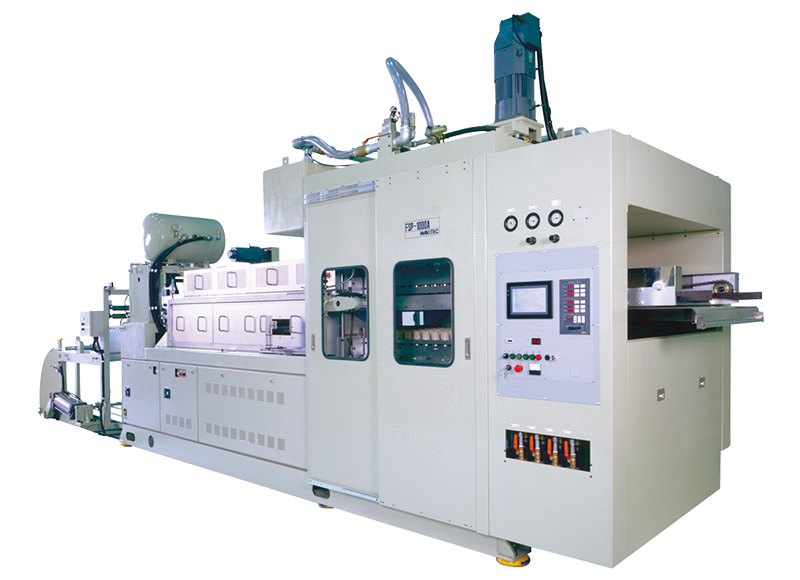
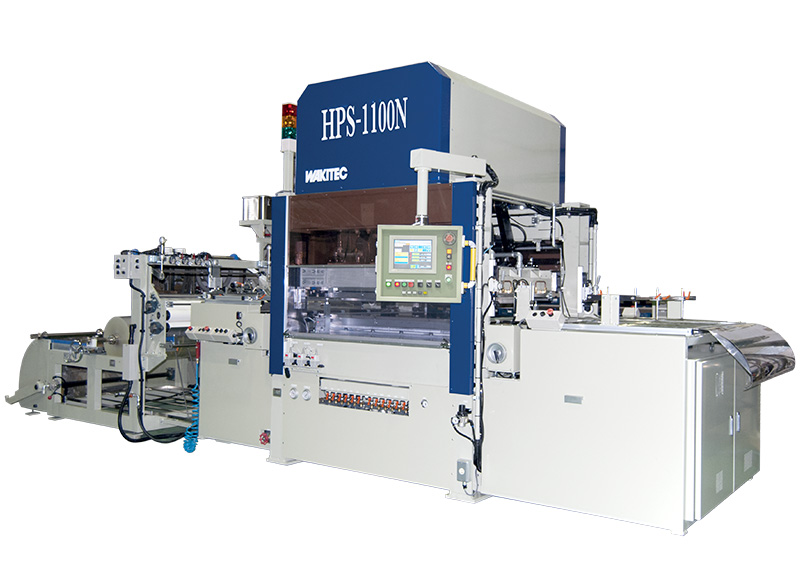
Industrial Trays and Blister Packs
In comparison to food containers, industrial trays and blister packs can generally be thought of as “multi-variety small-lot production.”
In such cases, a major deciding factor will be if a machine is capable of appropriately large (around 600mm) width and length (feed), offering mold cost-saving and minimized mold change time. An additional factor will be if the punching die uses a Thomson blade instead of a normal die, reducing both mold costs and running costs.
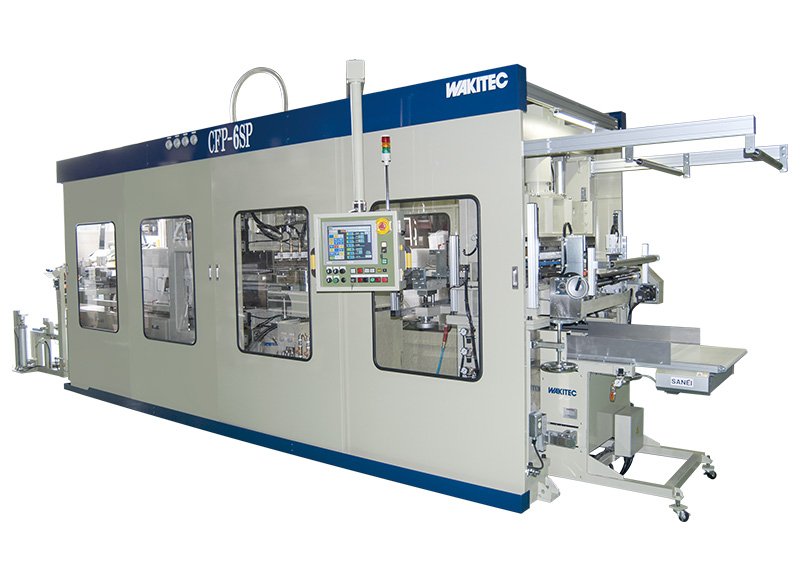
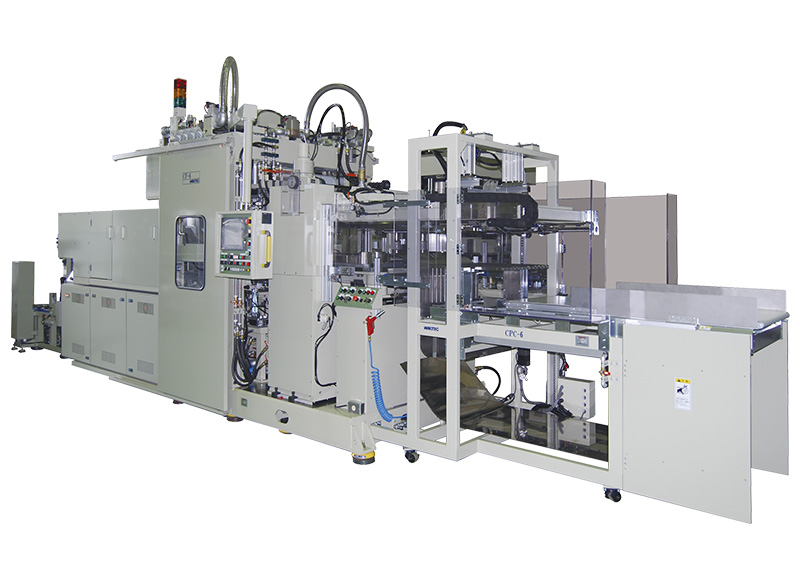
Lab (Research & Development) and Small-Lot Production
Research and development of new sheet materials, such as biodegradable sheets, has become a thriving field in recent years. In many cases, large-scale forming machines are excessive for research and development purposes, and there is a rising demand for compact forming machines that offer the same functions as commercial models.
WAKITEC has developed machines specifically for this purpose, which we call “test forming machines.” These convenient models are purchased by many of our customers, such as plant engineering companies and sheet manufacturers. Our test machines are also suited to small-lot production, such as product samples, and are popular with mold manufacturers for mold test use.
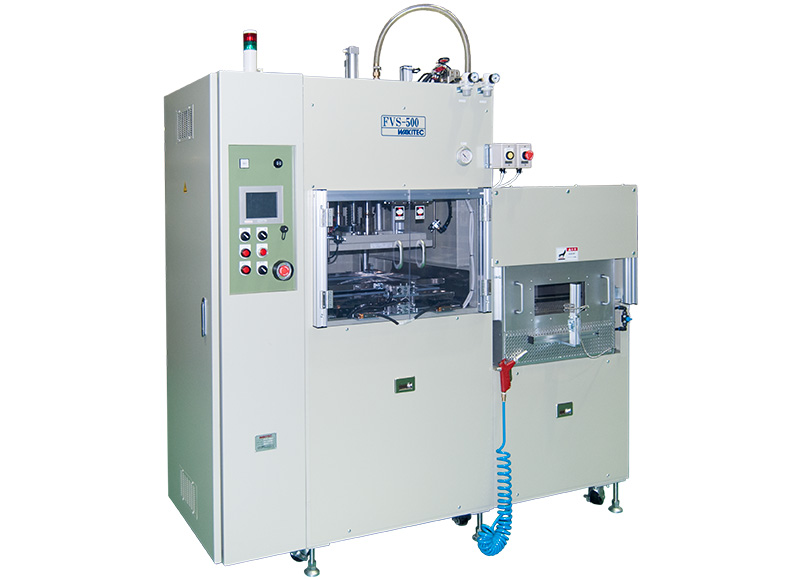
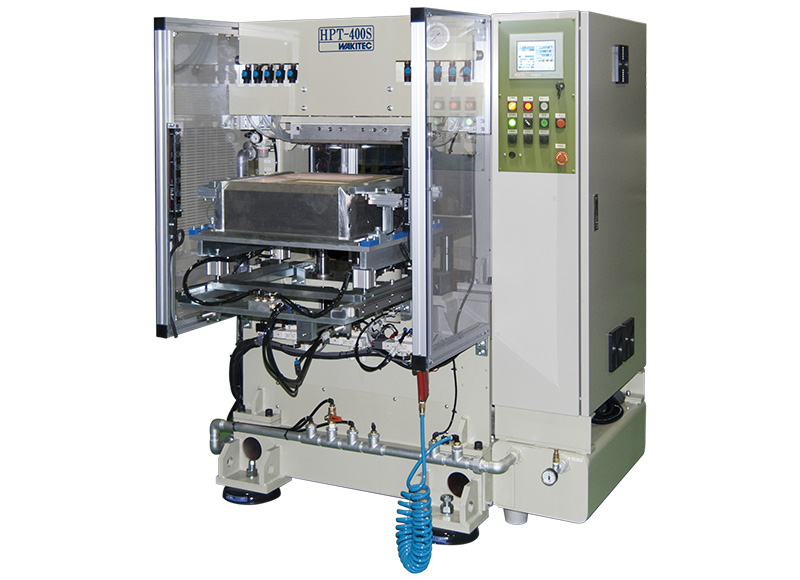
Forming Machine Line
Selecting a Trimming Machine (Puncher)
WAKITEC’s trimming machines offer the advantages of stable product feed, punching misalignment prevention, and high-cycle operation. In particular, our four-wheel drive system equipped with a product feed mechanism on both the entry and exit sides of the mold to prevent misalignment during punching, has been registered as a patent.
In addition to our main puncher described above, our lineup also includes our intermediate punchers WP-1000AM-10T(7T) and WSP-1000. These models are differentiated by their punching force and cycle rate.
Post-Processing
Selecting an Automation Device
The area of “post-processing”, which includes many customized elements that are specific to each customer, is a field where specialism in labor-saving and automation is in high demand. Since these requirements can be extremely difficult to summarize, we encourage customers to start by telling us what kind of things they want to achieve. WAKITEC will then propose optimal solutions.
Stacked Product Automatic Feeder
SI-1 TYPE (Preparing)